A contribution by Philipp Dasbach
The Problem
In archery, the repeatability of the entire shooting process is
crucial for a good result. I myself have owned an Olympic recurve bow with sights (aiming device) and stabilization system (weights for balancing, for smoother aiming) for several years.
Characteristic of this type of bow are the curved or backward bent ends of the bow, from where the English term “recurve” comes.
Unlike other shooting sports, where, for example, is shot over the rear sight and front sight, the sight of the recurve bow has only the front sight. Thus, the body posture and the stopping point of the bow (anchor point) form the second reference point of the recurve bow to define the direction in which the arrow flies. That is, even if the front sight always points to the gold (center of the target), but the bow is slightly different in your hand than it was when you shot it before, the arrow will hit somewhere else.
Therefore, many archers customize the grip of their bow with grip tape or modeling clay to craft a grip that is perfect and stable in their own hand. Since I was not satisfied with the grip of my bow, I decided to design my own grip, which also looks professional due to 3D printing.

Attempts to apply known knowledge
Before I designed the grip according to my ideas, I first wanted to copy the original grip of my bow, so that I could make the adjustments that seemed reasonable from this basis.
Due to my mechanical engineering studies at the University of Siegen, I am familiar with the use of CAD software and have confidently approached the design. However, two things caused me an unexpected amount of problems.
First, it took me a long time to design the many interlocking fillets of the handle. These fillets are very difficult to reproduce with software solutions from the mechanical engineering sector, since they usually have defined geometries. This took me some time, but also forced me to learn new features and capabilities of CAD software.
The second issue that cost me a few tries in 3D printing is the measurability of the hard-to-define geometries.
Since the handle has only a very narrow, straight edge, it was very difficult to measure the position of the hole, bevels and radii. However, it is important for the attachment of the grip piece to the sheet that the geometry of the grip piece corresponds exactly to the geometry of the receptacle provided for it on the sheet. Since I could only roughly estimate many dimensions, I had to approach the correct geometry step by step through trial and error.
During this trial and error, I was able to learn a lot about 3D printing from the staff and makers in the Fab Lab. Above all, they helped me find the ideal slicer settings for my part and the right material. In addition, the Fab Lab works with different CAD programs, all of which have their strengths for different problems.
Prototyping
After four attempts I had copied the original grip of my bow sufficiently well and started with attempts to adapt the grip geometry to my hand. In the process, I tried a total of five different versions.
First, I made changes that seemed logical to myself to stabilize certain areas of the hand to prevent it from slipping back and forth. On the other hand, I combined this with geometries of grips from different manufacturers to arrive at my individual and optimal grip.
Currently, I have mounted a version of the grip on my bow, in which I have rounded some disturbing edges of the original grip and minimize the back-and-forth slipping by changing the angle of the contact surface.

Satisfied, but surely there’s more?!
I definitely achieved my goal of getting a better grip than the old one. Whether I have already found the ideal solution, I do not know, because there are still some geometries that I could try.
In the meantime, I uploaded the latest version of the grip to Thingiverse and hope to run into an archer who also uses my grip. Overall, I have to say that through the exchange in the Fab Lab I got ideas and tips that I would never have come up with on my own.
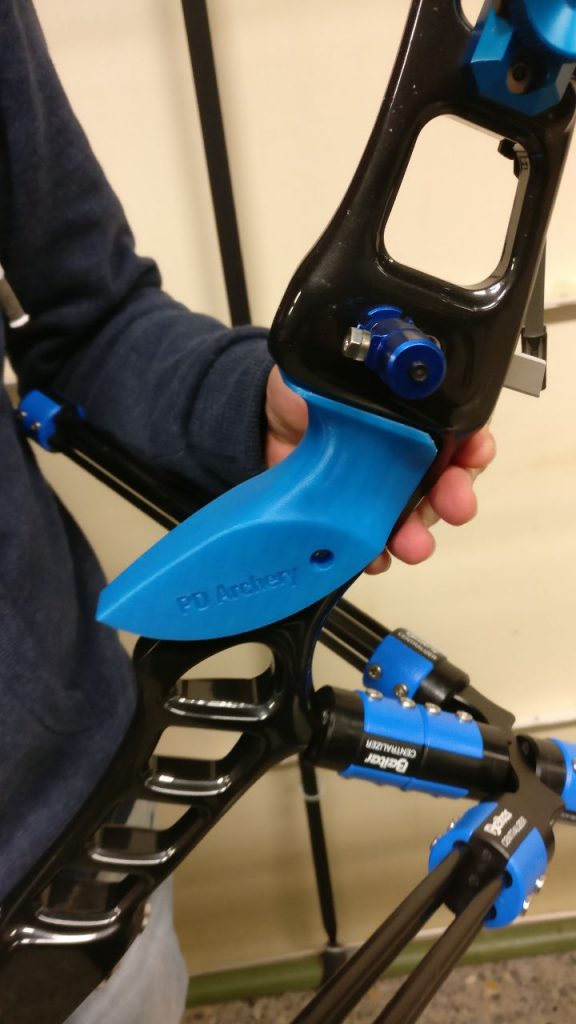
Copyright Pictures: Philipp Dasbach